Today, their production is more flexible, and it disposes accurate data in real time, what is reflecting also in the field of the performance indicators.
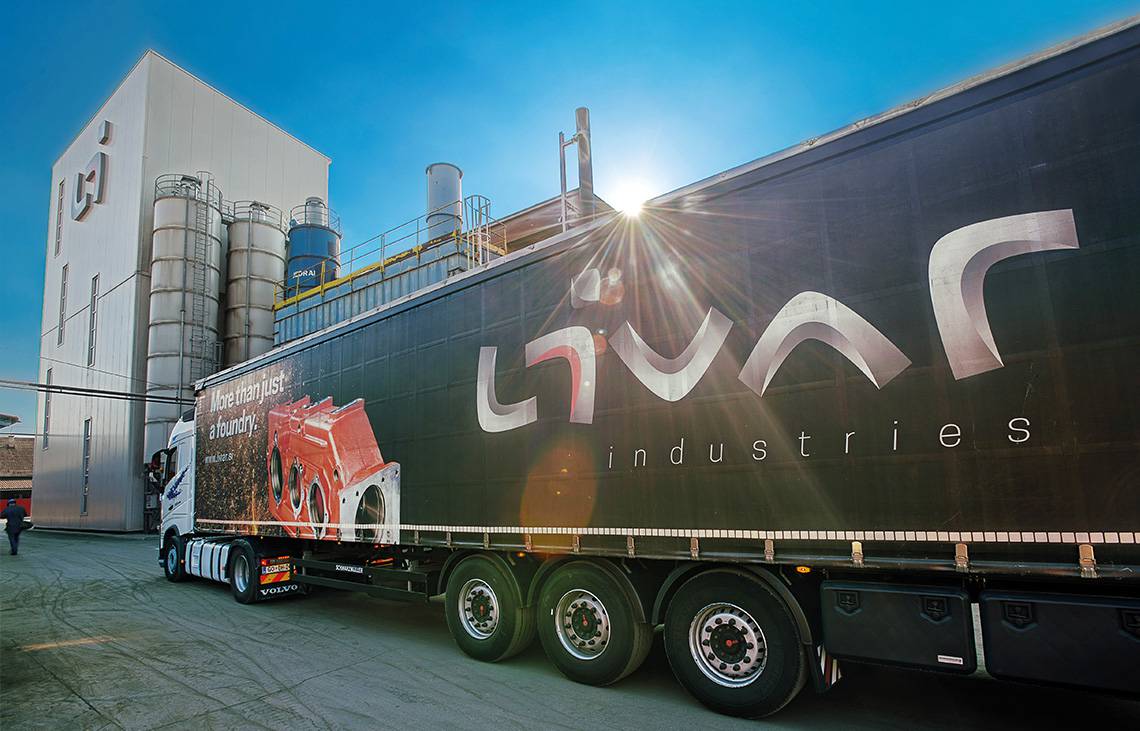
The company Livar is the largest foundry of iron castings in Slovenia, specialized in the production of iron cast products and nodular iron with its own mechanical processing. The company’s strategy is focused to the future important investing into optimization, automation, and digitalization of production processes, as well as into other business fields of the company.
Recently, the company completed the first phase of digital transformation of the mechanical processing plant, thus enabling, in every moment, a perfect traceability of production processes, as well as of a complete material stream, and consequently the monitoring of the production.
Real time insight in production
The company’s management, who is oriented to the production, assures, on daily basis, the monitoring of vital production indicators and coordinates the realization of corrective measures. The decision of the management to introduce a step-by-step digital transformation has arisen from their past challenges, appearing, mainly, in the domain of the production process planning, monitoring, and effectiveness of production. By introducing the solutions from the variety of solutions, which a digital transformation of production can provide, the management succeeded to implement an integrated solution, with which they assured effective allocation of working tasks over the working places, the monitoring of material stream and of inter-phase stocks, eliminated manual entries of data, completely automated the collection of key data directly from machines, and they completely removed paper from the production of mechanical processing.
»We have established an entirely paperless production, thus that the working tasks are entirely electronic. Preliminary works, planning, performance of individual operations as per individual working task, and the finishing works, and quality assurance are also digitalized. Thus, we assured a complete monitoring of the current condition of machines, monitoring of the achievement of norms, monitoring of all standstills, including the causes and times of standstills, planning and supervision of consumption of material and tools as per machines, and monitoring of the manufactured quantities, including the adequate quality”, told us Sašo Malerič, manager of the Division of mechanical processing of the company Livar.
Real time manufacturing operations wiith Sinapro.IIoT.MES
At the beginning of the year 2018, the company’s management addressed a demand for assistance to the company Kolektor Sisteh and started their digital transformation and implementation of the system Sinapro.IIoT.MES. A comprehensive understanding of the production systems and of the managing of technologies in the process industry and in the bulk industry was indispensable for the successful performance of the first phase of digital transformation. Kolektor Sisteh contributed to this transformation their years-long experience in the domain of automation and computerization, and they adapted their own solution, which meets, successfully, the needs of the specificity of work and the requirements of the company Livar, thus enabling higher effectiveness and satisfaction of all the employees.
Thus, the solution comprises automated collection of data and information on the completed work in real time directly from machines, the machine lines, and from individual units for each individual working place. At the same time, the solution provides, at the right time, an automated and intelligent allocation of working tasks over the machines, a bi-direction communication with the business system ERP, and the assurance of the transfer of key instructions and information to the staff to the corresponding working place. In this way more precise key information about the events in the production process are always available to the employees. Thus, the system becomes more transparent and provides an additional control for the elimination of standstills, and consequently it improves a general working discipline and relationships between the employees in the company.
Today, their production is more flexible, and it disposes accurate data in real time, what is reflecting also in the field of the performance indicators.
Sašo Malerič, manager of the Division of mechanical processing of the company Livar:
The implementation of the system Sinapro.IIoT.MES enabled to the company Livar an important increase in the productivity of the production processes in the Division of mechanical processing without additional organizational changes.
Back